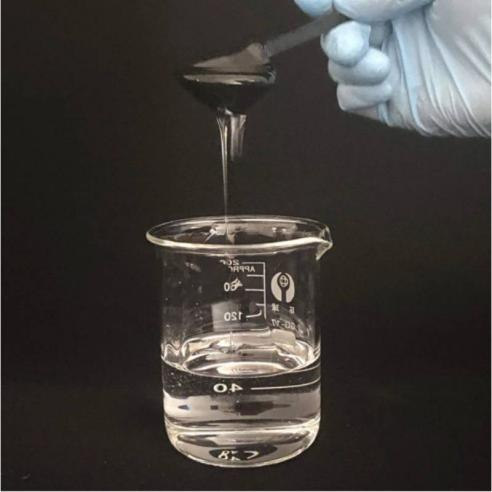
Acrylic resins, as a versatile class of polymers, have found extensive applications across industries ranging from coatings and adhesives to plastics and textiles. Among the diverse variants, three major types stand out for their distinct properties and functional roles: hydroxy acrylic resins, thermoplastic acrylic resins, and thermosetting acrylic resins. Each type, shaped by its chemical structure and polymerization process, offers unique advantages that cater to specific industrial needs.
Hydroxy Acrylic Resins: The Versatile Binder with Cross-Linking Potential
Hydroxy acrylic resins are defined by the presence of hydroxyl (-OH) groups in their molecular structure, a feature that endows them with remarkable adaptability. These hydroxyl groups serve as reactive sites, enabling cross-linking with various curing agents such as isocyanates, melamine-formaldehyde, or epoxy resins. This cross-linking capability transforms the resin into a durable, high-performance material, making it a cornerstone in the formulation of high-quality coatings.
In practical applications, hydroxy acrylic resins are prized for their excellent adhesion to substrates, weather resistance, and gloss retention. They are commonly used in automotive coatings, industrial finishes, and architectural paints, where durability and aesthetic appeal are paramount. The ability to adjust the hydroxyl content during synthesis allows manufacturers to tailor the resin’s properties—from flexibility to hardness—meeting the demands of diverse environments, whether exposed to harsh weather or chemical abrasion.
Thermoplastic Acrylic Resins: The Heat-Moldable Workhorse
Unlike their hydroxy counterparts, thermoplastic acrylic resins lack reactive functional groups and do not undergo cross-linking during processing or use. Instead, their properties are determined by their molecular weight and glass transition temperature (Tg). These resins soften when heated and harden upon cooling, a reversible process that allows for easy molding, extrusion, or thermoforming.
Thermoplastic acrylic resins are celebrated for their clarity, UV resistance, and ease of processing. Their low viscosity in molten form makes them ideal for applications such as plastic sheets, signages, and consumer goods where transparency and formability are key. Additionally, their resistance to yellowing under sunlight ensures long-term aesthetic stability, a trait highly valued in outdoor products. However, their lack of cross-linking limits their chemical and heat resistance compared to thermosetting types, confining them to less demanding environments.
Thermosetting Acrylic Resins: The Heat-Cured Powerhouse
Thermosetting acrylic resins are engineered to undergo irreversible cross-linking when exposed to heat, catalysts, or radiation. This cross-linking forms a dense, three-dimensional network, imbuing the material with exceptional heat resistance, chemical stability, and mechanical strength. Unlike thermoplastic resins, once cured, they cannot be reshaped by heating, making them suitable for high-performance applications where permanence is critical.
These resins are widely used in aerospace coatings, electrical insulation, and high-temperature industrial components. Their ability to withstand extreme temperatures and harsh chemicals, combined with strong adhesion to metals and ceramics, makes them indispensable in demanding sectors. The curing process can be fine-tuned—through temperature control or catalyst selection—to achieve specific properties, balancing speed of production with final performance.
Bridging the Gaps: Complementary Roles in Industry
While each type of acrylic resin has distinct characteristics, their roles often overlap and complement one another in industrial formulations. For instance, hydroxy acrylic resins may be blended with thermosetting components to enhance flexibility without sacrificing durability, or thermoplastic resins might be used as modifiers to improve the processability of thermosetting systems.
In conclusion, hydroxy acrylic resins, thermoplastic acrylic resins, and thermosetting acrylic resins represent the backbone of the acrylic resin family, each contributing unique strengths to modern manufacturing. Understanding their structural differences and functional capabilities is essential for selecting the right resin for a given application, ensuring optimal performance, efficiency, and longevity in the final product. As technology advances, ongoing innovations in resin synthesis continue to expand their potential, solidifying their place as indispensable materials in the global industrial landscape.