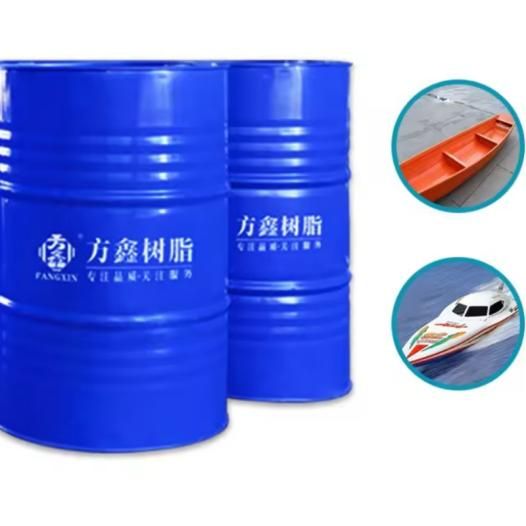
Unsaturated Polyester Resins (UPR) have established themselves as a cornerstone material in various industrial sectors, from construction and automotive manufacturing to marine engineering and electrical components. Derived from the condensation of unsaturated dicarboxylic acids or anhydrides with diols, UPRs are thermosetting polymers that cure through cross-linking reactions, forming rigid, durable structures when combined with reinforcing materials like glass fibers. Their widespread adoption stems from a unique blend of properties, yet they are not without constraints. This article explores the key advantages and limitations of UPRs in industrial applications.
Advantages of Unsaturated Polyester Resins in Industrial Use
1. Cost-Effectiveness
One of the primary drivers behind UPRs’ popularity is their low production and processing cost compared to alternative thermosetting resins such as epoxy or phenolic resins. The raw materials for UPR—including phthalic anhydride, maleic anhydride, and ethylene glycol—are abundant and relatively inexpensive, making UPR an economical choice for large-scale industrial production. This cost advantage is particularly critical in sectors like construction (e.g., fiberglass-reinforced panels) and consumer goods, where material expenses directly impact profitability.
2. Versatile Processing Capabilities
UPRs offer exceptional flexibility in manufacturing, accommodating a wide range of processing techniques that suit diverse industrial needs. They can be molded using methods such as hand lay-up spray-up, compression molding, resin transfer molding (RTM), and pultrusion. This versatility allows manufacturers to produce complex shapes, large components, or intricate designs with relative ease. For example, in marine applications, UPRs are often shaped into boat hulls via hand lay-up, a cost-effective process that requires minimal specialized equipment. Additionally, UPRs cure at room temperature with the addition of peroxides (e.g., methyl ethyl ketone peroxide) and accelerators, eliminating the need for high-temperature curing ovens and reducing energy consumption.
3. Balanced Mechanical Properties
In reinforced forms (e.g., with glass fibers), UPRs exhibit excellent mechanical strength, including high tensile and flexural strength, which rival those of traditional materials like metal or wood. This makes them ideal for structural applications such as automotive body panels, pipe systems, and building cladding. Moreover, UPR composites offer a favorable strength-to-weight ratio, contributing to lightweight designs—an advantage in industries like aerospace and transportation, where fuel efficiency is critical.
4. Chemical and Corrosion Resistance
UPRs demonstrate strong resistance to many chemicals, including acids, alkalis, and solvents, depending on their formulation. This property makes them valuable in industrial settings such as chemical processing plants, where they are used to fabricate storage tanks, pipelines, and protective linings. Unlike metals, which are prone to rust and corrosion, UPR-based components maintain their integrity over time in harsh chemical environments, reducing maintenance costs and extending service life.
5. Electrical Insulation and Dimensional Stability
UPRs are inherently good electrical insulators, making them suitable for electrical and electronics applications, such as switchgear enclosures, cable trays, and insulating panels. Their low thermal conductivity further enhances their utility in electrical systems. Additionally, when properly formulated, UPRs exhibit minimal shrinkage during curing, ensuring dimensional stability in precision components—an essential trait in industries like aerospace and medical device manufacturing.
Limitations of Unsaturated Polyester Resins in Industrial Use
1. Limited Thermal Resistance
A major drawback of UPRs is their poor performance at high temperatures. While they can withstand moderate heat (typically up to 80–120°C), prolonged exposure to temperatures exceeding this range causes softening, dimensional distortion, and a decline in mechanical properties. This limits their use in high-temperature industrial environments, such as engine compartments, industrial ovens, or exhaust systems, where materials like epoxy resins or thermoplastics (e.g., PEEK) are more suitable.
2. Susceptibility to Water Absorption
UPRs are hygroscopic, meaning they absorb water over time, especially in humid or submerged conditions. This absorption can lead to swelling, reduced mechanical strength, and increased brittleness, compromising the integrity of components. While water-resistant formulations exist (e.g., using isophthalic acid), they are more expensive and do not eliminate the issue entirely. As a result, UPRs are less ideal for applications requiring long-term water immersion, such as underwater pipelines or marine structures exposed to constant moisture.
3. Brittleness and Low Impact Resistance
Unreinforced UPRs are inherently brittle, with low resistance to impact or sudden stress. Even when reinforced with fibers, they may crack under extreme mechanical loads or sudden impacts, limiting their use in high-stress applications like heavy machinery parts or structural components subject to dynamic forces. This brittleness can be mitigated by blending with elastomers or using advanced reinforcing fibers (e.g., carbon fibers), but such modifications increase production costs.
4. Environmental and Health Concerns
The curing process of UPRs often involves the release of volatile organic compounds (VOCs), such as styrene—a common cross-linking monomer. Styrene is not only flammable but also poses health risks, including respiratory irritation and long-term toxicity, requiring strict ventilation and safety measures in manufacturing facilities. Additionally, UPRs are thermosetting polymers, meaning they cannot be melted or recycled easily, contributing to waste management challenges in industries striving for sustainability.
5. Sensitivity to UV Degradation
Exposure to ultraviolet (UV) radiation—such as sunlight—can cause UPRs to degrade over time, leading to discoloration, surface cracking, and loss of mechanical properties. This limits their use in outdoor applications without protective coatings (e.g., gel coats or UV stabilizers). While additives can enhance UV resistance, they add complexity and cost to the manufacturing process, and their effectiveness diminishes over extended periods.
Unsaturated Polyester Resins (UPRs) occupy a significant position in industrial applications, thanks to their cost-effectiveness, versatile processing, and balanced mechanical and chemical properties. They excel in sectors ranging from construction to automotive manufacturing, where their affordability and adaptability drive innovation. However, their limitations—including poor thermal resistance, water absorption, brittleness, and environmental concerns—restrict their use in high-performance or harsh-environment scenarios.
As industrial demands evolve, research into UPR modifications (e.g., nanocomposite reinforcements, bio-based monomers, or low-VOC formulations) aims to mitigate these drawbacks. By addressing issues like heat resistance and recyclability, UPRs can continue to compete with advanced materials while retaining their cost and processing advantages. Ultimately, the effective use of UPRs in industry hinges on selecting the right formulation for specific applications, balancing performance requirements with practical constraints.